"A UNIQUE FRENCH KNOW-HOW THAT ALLOWS AUDACITY"
Since 1981, La Maison FREE LANCE has been celebrating French craftsmanship through its culture, the transmission of its boot-making know-how and its love of prestigious materials.
FREE LANCE reinvents the lines by magnifying the heritage.
Creations with a strong style, which embody the creative power proper to FREE LANCE in the smallest details, are born.
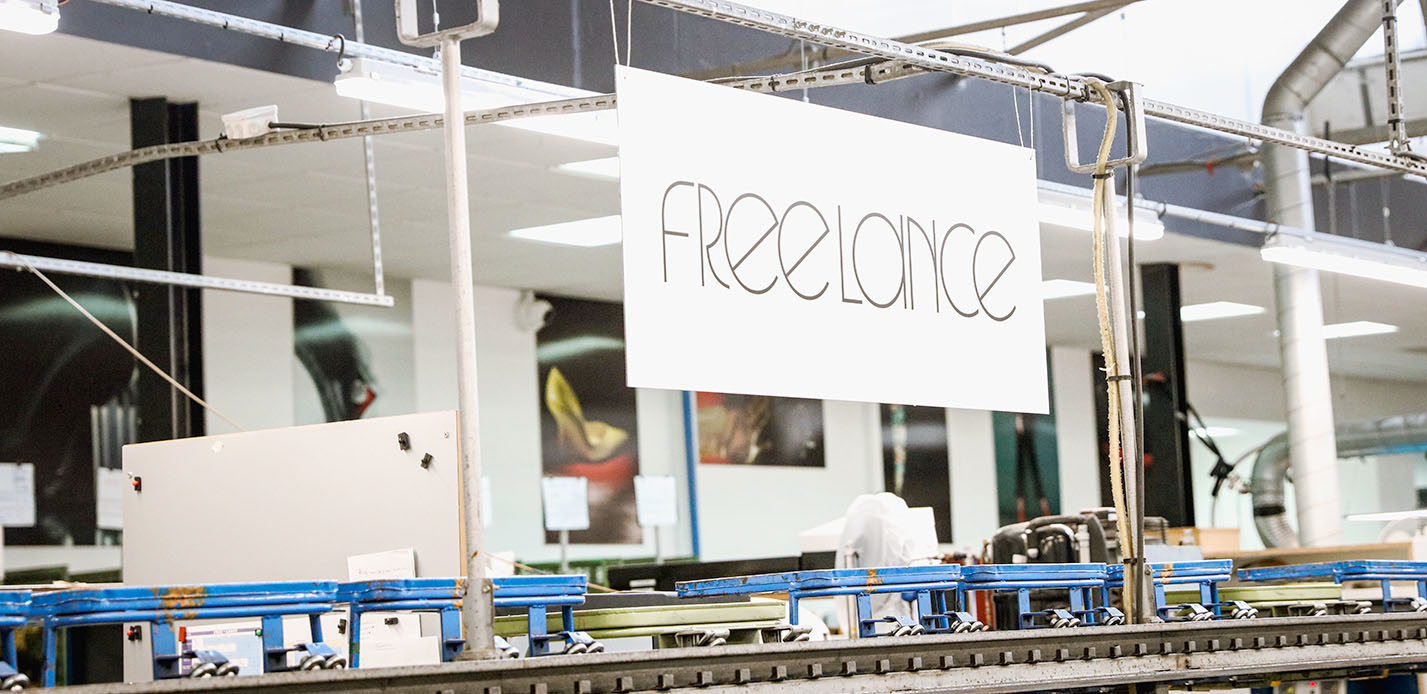
THE FRENCH CRAFTSMAN
Far from the hustle and bustle of Paris, Free Lance is based in La Gaubretière in western France for over a century.
The original cobbler’s shop from 1870 has been expanded and developed into a sophisticated factory brimming with rarefied know-how, one of the few in France to still possess the craftsmanship handed down by artisanal shoemakers from generation to generation.
Going behind the scenes at FREE LANCE means discovering the complex and fascinating job of bootmaker, which can take up to 150 steps for some creations.
Each pair, upper, sole, and heel will pass through the agile and skillful hands of dozens of men and women who harness their craft with real passion.
One single watchword unites them: perfecting each creation to offer unparalleled comfort and style.
A STORY OF SHAPES
Based on the designer’s sketch, a former takes a block of wood and sculpts it into the shape that will create the volume and the very essence of the shoe.
This sculpted wooden shape is the initial prototype.
Once validated, the shape is then reproduced in plastic and adapted to all the necessary sizes.
Those shapes will serve as the foundation on which the future shoe will be assembled.
The pattern maker/model maker will then transcribe the designer’s two-dimensional sketch into a three-dimensional model known as a shoe last.
The shoe last is a foot-shaped model that the pattern maker can draw on.
This stage makes it possible to match together the various pieces that will constitute the upper and to ensure the overall cohesion and future fit of the shoe.
The pattern maker/model maker then breaks down the design from the shoe last to obtain a flat pattern for each of the constituent parts of the shoe.
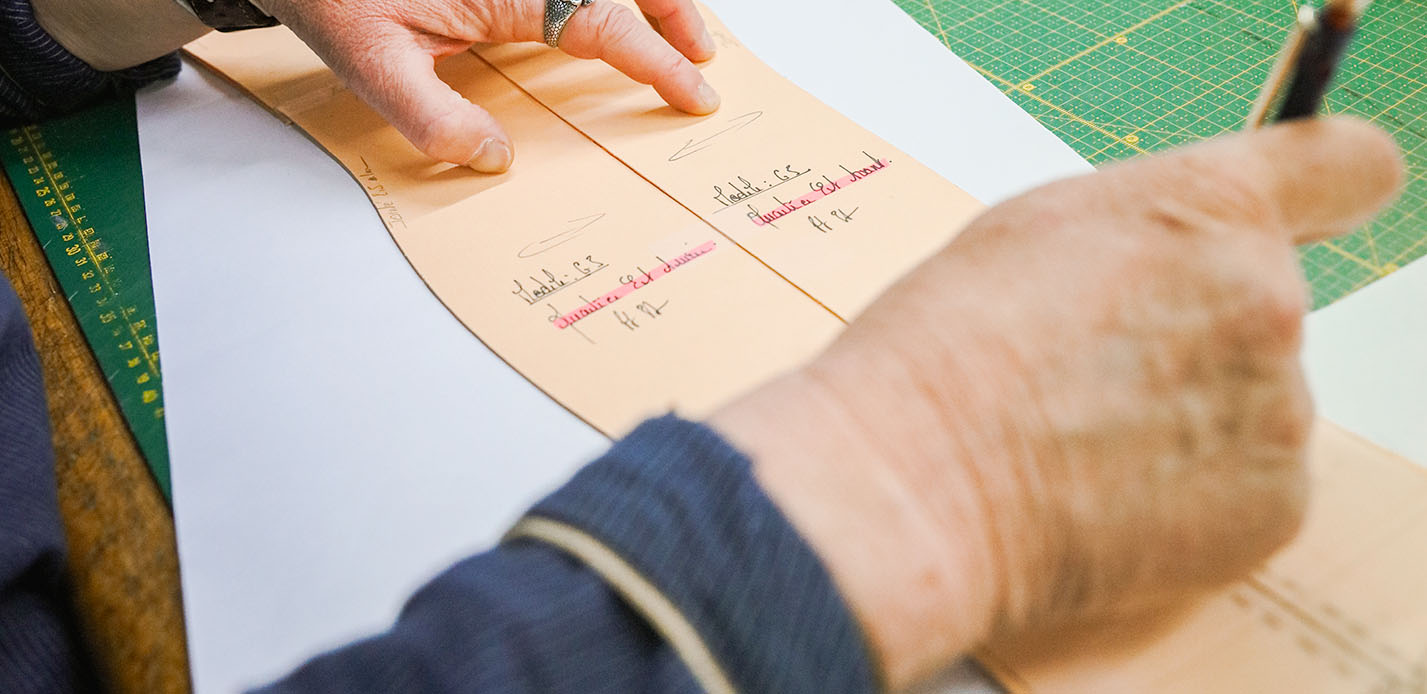
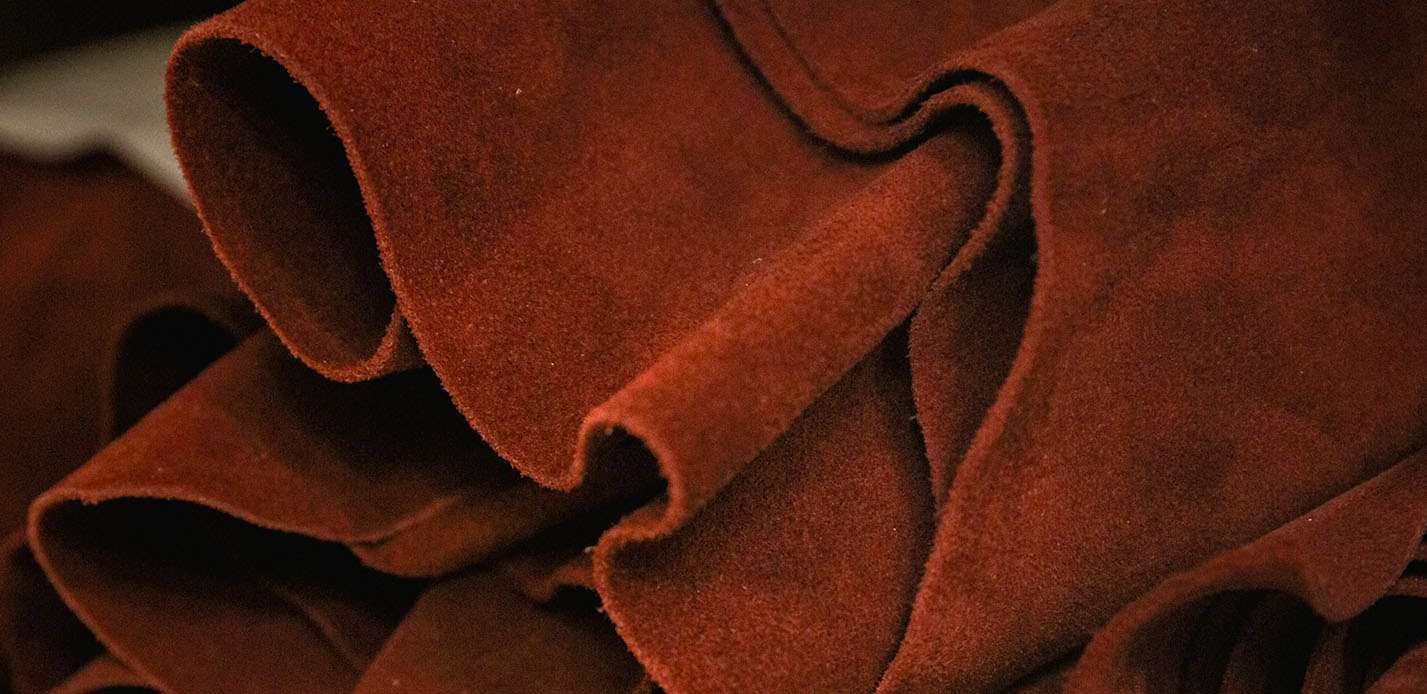
THE LOVE OF HIDES
The selection of the skins is a crucial step.
Dyed beforehand according to the designers' wishes, they guarantee compliance with European practices and environmental standards. FREE LANCE works exclusively with Italian tanneries that have been audited and certified by the "Leather Working Group" and/or "ISO 14001", international certifications that control the management of water resources and the treatment of waste from tanning before it is sent to treatment plants.
Each skin arrives at the factory in its entirety and is entitled to the same treatment. We turn them, we turn them over, we caress them, we feel them, we stretch them, we look at them with the same passion and ambition, that of transforming a few square centimeters of skin into a beautiful pump or a boot that fits the ankle like a glove.
THE PRECISION OF THE CUT
he pieces needed for the production are meticulously selected with the help of patterns and then cut by hand with great dexterity. Each piece, each reinforcement, each lining, will be carefully cut to the millimeter by the cutter's agile hands.
Concerned about respecting the work done and the raw materials, FREE LANCE reuses the leather scraps. In this respect, some pieces will also be cut thanks to innovative tools such as the digital cutting machine in order to optimize the placements.
The cutter has a perfect knowledge of the material, which allows him to choose the best full grain leathers. After a rigorous selection, he stretches them with all his strength in length and width to ensure an incomparable quality of material whose fineness, colour and suppleness do not give way to its solidity

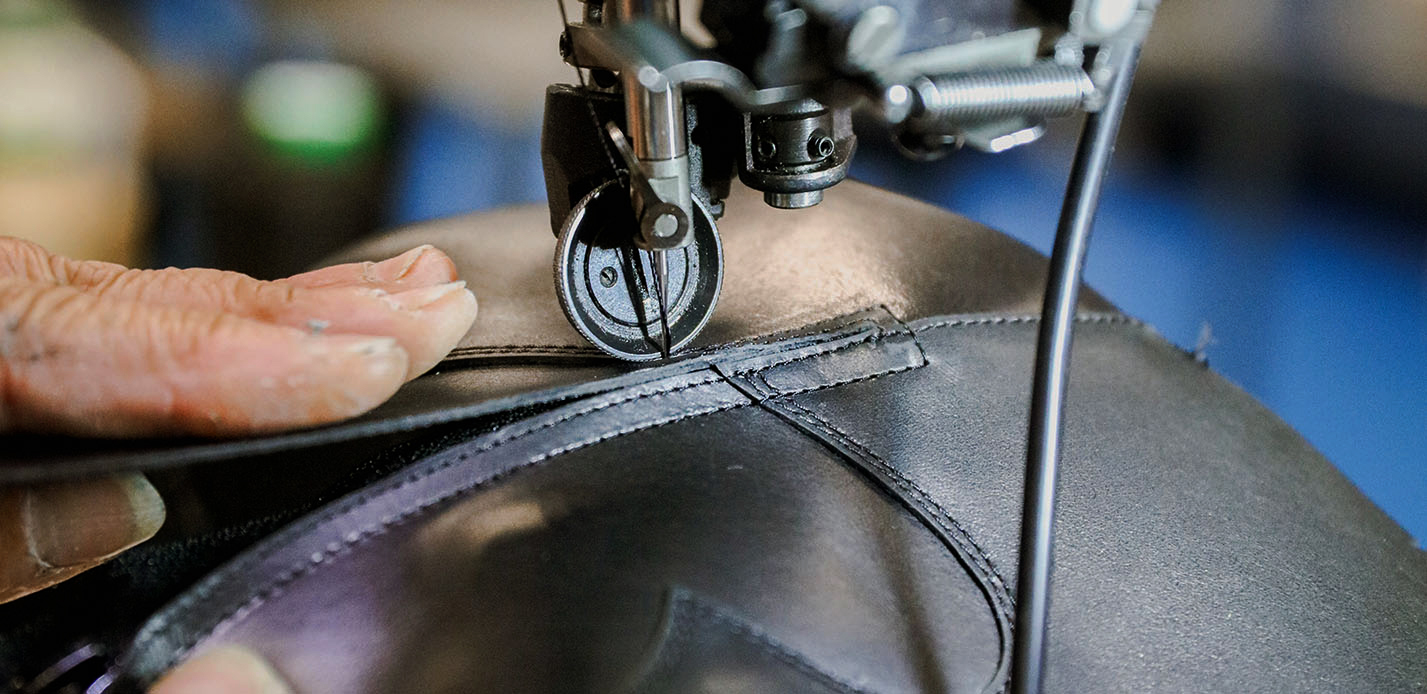
THE DEXTERITY OF THE STITCHING
After the cutting stage, it is time for the stitching, sewing, and embroidery done by a few experts using traditional sewing machines. All the sections will be joined together to form the upper.
Like the other jobs, stitching requires an exceptional degree of skill and dexterity honed and perfected over years of practice.
The steps involved are long and complex: tracing, trimming, jointing, assembling, fitting reinforcements...
All of which bears testament to the know-how of the stitcher, whose nimble fingers work steadily, evenly, and meticulously.
At the end of this process, the upper is three-dimensional once again. Meanwhile, other workers have been busy developing the piece that will form the backbone of the shoe: the insole (the part under the foot where the sole and the upper are stitched together).
THE DIFFERENT STITCHING TECHNIQUES
The Goodyear welt
The Goodyear welt is a double-stitched seam.
The first stitch connects the upper, the insole and the welt. The second one joins the welt to the outsole.
This stitching technique ensures unparalleled sturdiness.
The Blake stitch
The Blake stitch is a single seam joining the outsole and the upper.
This stitching technique allows for a certain finesse.
Cementing
These days, the most widely used manufacturing method worldwide is cementing, also known as gluing.
It is a technique that employs various adhesives to attach the upper to the sole of the shoe.
This process makes it possible to produce softer shoes.
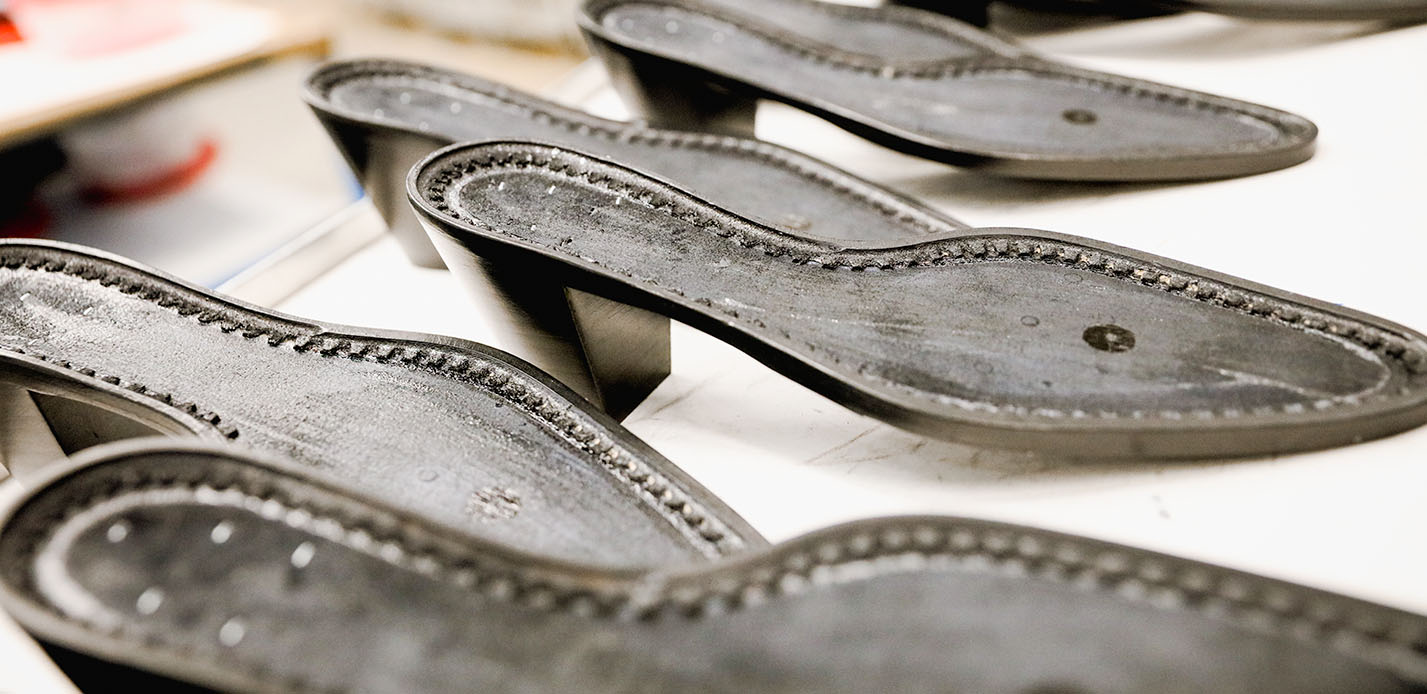
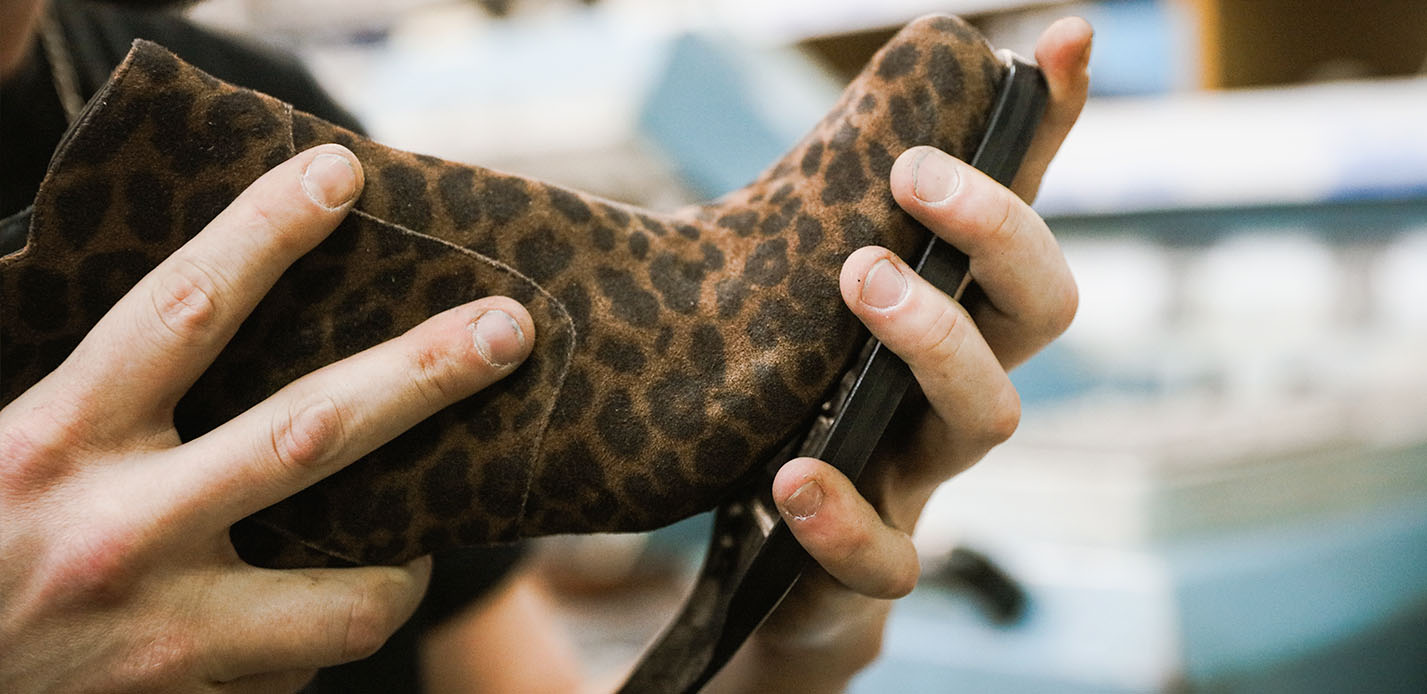
THE ASSEMBLY TECHNIQUE
Assembly is a crucial step that consists of placing the upper on the shoe last, stapling the insole, and next attaching the sole and heel.
Each shoe will then follow a defined path, including exposure to extremely hot and cold temperatures along the way, so that the leather—a living material—is tamed and takes on its best shape. The shoe will be passed from hand to hand, workstation to workstation, and each skilled artisan will carefully stitch, glue, tap, punch, assemble, sand, card, and wax each shoe before adding the manufacturer’s signature.
This signature is a source of pride, a declaration of our pursuits of perfection, and an ultimate bulwark against counterfeiting. On the sole, it is embroidered, gilded, in gold, in silver, it alone lets you recognize your unique pair.
THE ART OF PAMPERING
At FREE LANCE, the final stage in our shoemaking process is one we have dubbed “pampering”. That name attests to the passion and love that our skilled artisans bring to their craft.
In this part of the workshop, they make their finishing touches to their creations: rubbing, brushing, and waxing. Here, the noise of the sewing machines is just a faint whirring in the distance. The sounds heard here are those of rustling paper and the gentle brushing of leather.
Each shoe undergoes meticulous quality control. If the shoes pass, only then will they be placed in a box and be scrupulously wrapped in recycled silk paper, so they can find their way to the dressing room of a woman who will watch them acquire a patina and become more beautiful with the passing of time.
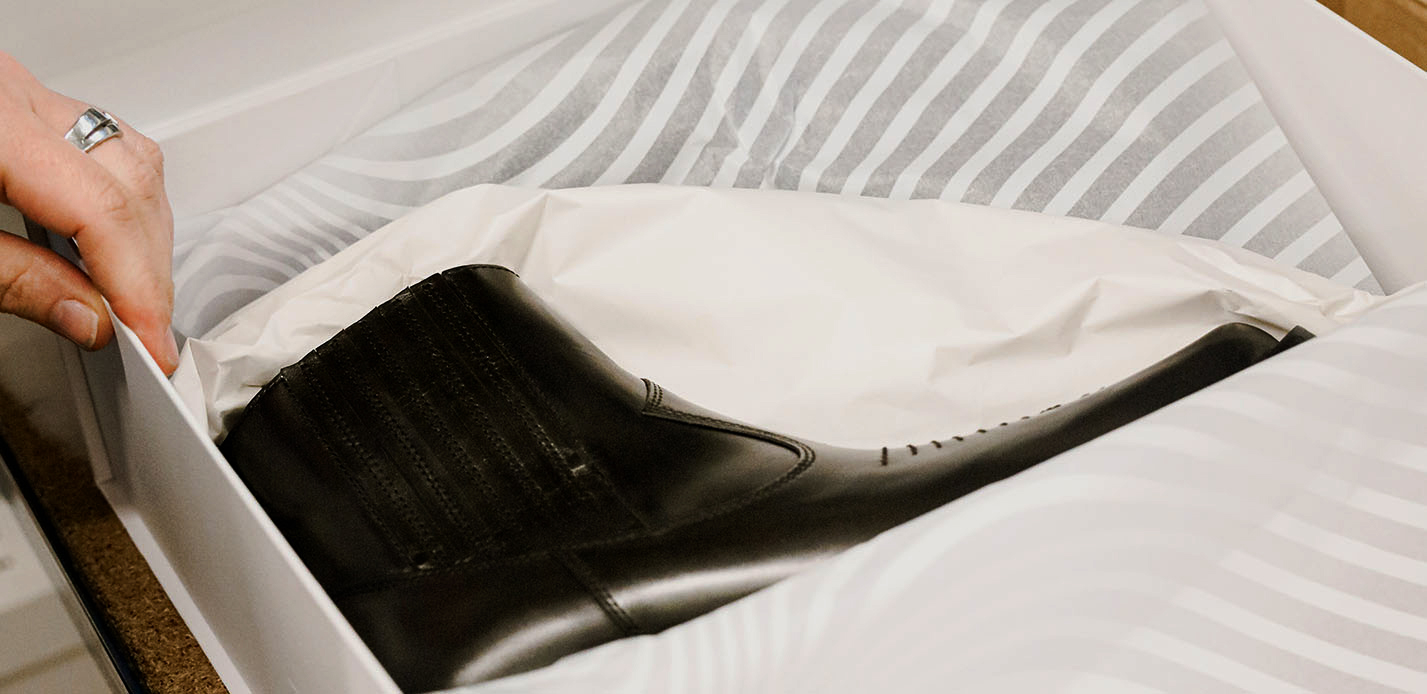